”真鍮板から車両を作る”と題してこれまで製作の過程を紹介してきたキハ52・キハ25が塗装を終えほぼ完成状態となりましたので改めて紹介させていただきます.その製作過程を紹介した記事の中で,私は車体の「光の反射具合」を考慮することが作品が実感的か否かに影響を与えるのではないかと考え,設計や製作の中ではその点に留意して製作を行いましたが,車体の光の反射具合は塗装して初めて結果が明らかになります.そこで今回はその点に注目して紹介をさせていただきたいと思います.
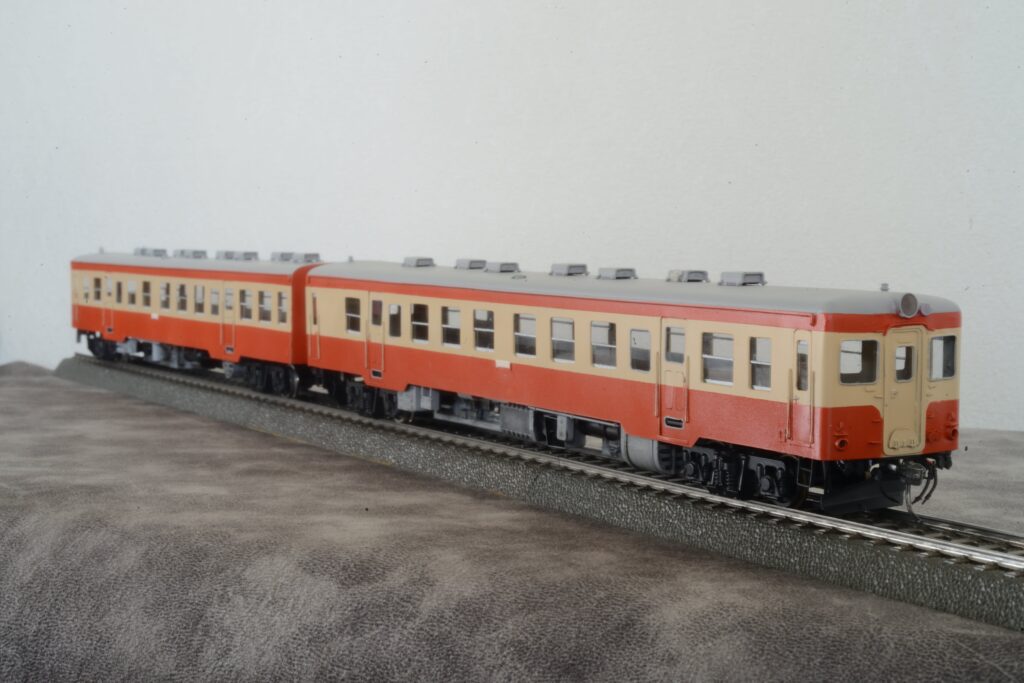
・ 作品の概要
<キハ52>
キハ52の車体は前面も含めて全て0.3㎜の真鍮版を使用しています.床板は0.8㎜の真鍮板を使用しており,床下機器は日光モデルのダイキャスト製の製品とフェニックス模型店のホワイトメタル製のパーツを混用しており,動力は天賞堂製のコアレスパワートラックll,台車(DT22)はエンドウ製を使用しています.パワートラック付属のウエイトは未使用で重量は約310gで,平坦線であれば無動力のキハ25を牽引しての走行が可能です.寒冷地仕様として先頭部には複線用のスノウプラウを取り付けました.カプラーは天賞堂製のkadee #16タイプを使用しています.床下機器は以前組み立てたバラキットの素養した残部品を使用しているため厳密には実車のとおりではありません.
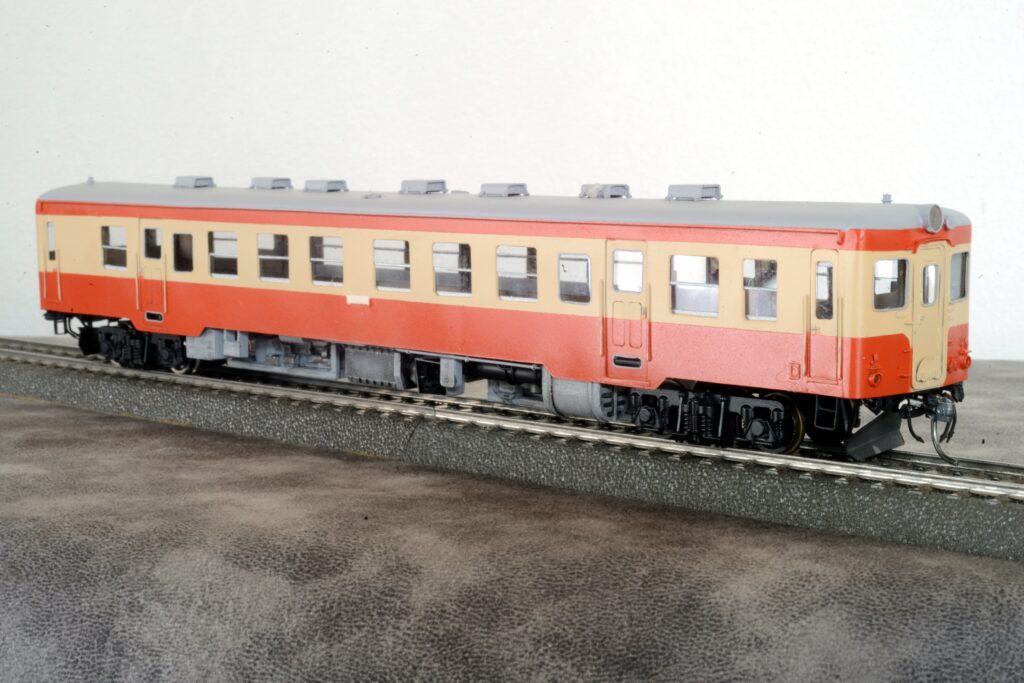
<キハ25>
キハ25の車体構造はキハ52とほぼ同一ですが,こちらは前面にフェニックス模型店製のプレス製のパーツ(1980年頃の製品)を使用しています.動力は装備しておらず,台車はエンドウ製のDT22(プレーン車軸)を使用しています.重量は290gで,動力車のキハ52とそれほどかわりません.
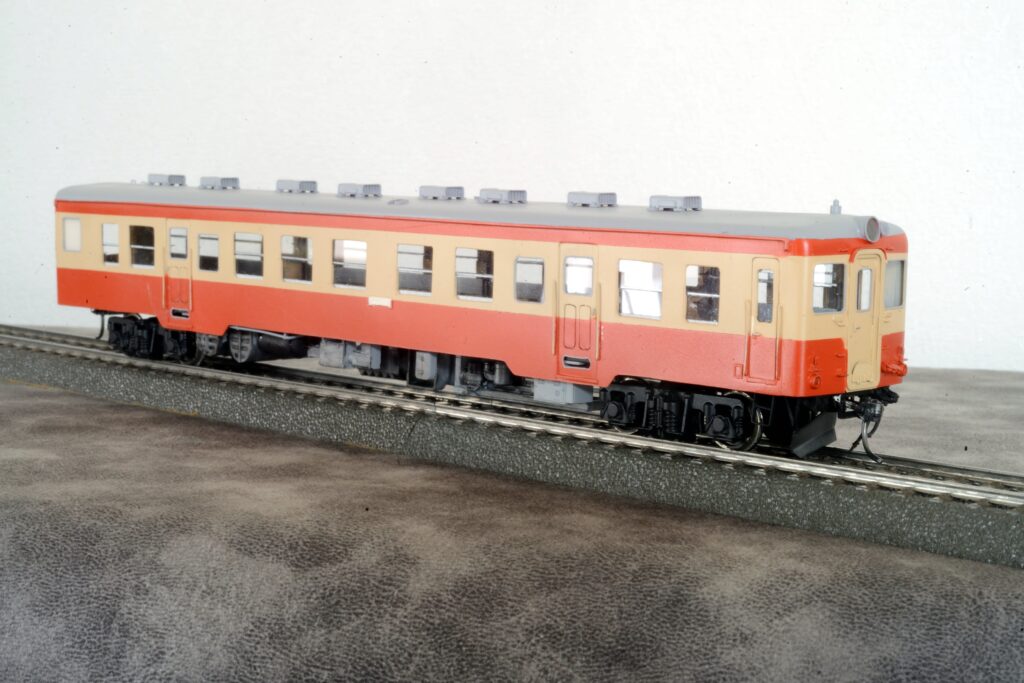
・ 前面の印象
前述のようにキハ52は車体前面も含めて全て自作したのに対し,キハ25は1980年ごろに購入したフェニックス模型店製と思われるプレス製の前面パーツを使用しています.そのため両者では前面の表情がやや異なります.自作のキハ52については今回詳細な寸法を記載した資料は手に入りませんでしたので,全面窓の大きさ等わずかな資料と写真から寸法を決めて製作しています.
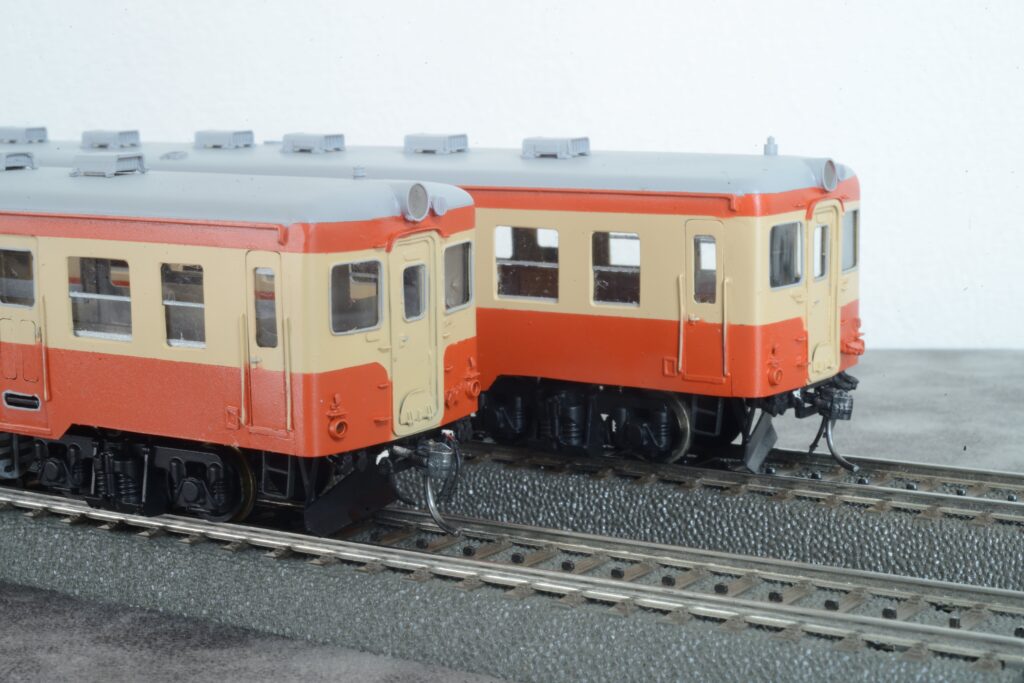
運転室窓の寸法は大きさが710×710㎜であるという資料がありました.これは1/80に換算すると8.875㎜となりますが,これは構体の開口寸法と思われますので実際の設計(罫書き)寸法は8.5㎜としました.結果的にはノギスによる実測値で8.4㎜に仕上がっています.一方フェニックス模型店製の製品は実測で8.75㎜弱となっています.寸法差としては僅かですが,この差が前面の表情の差に現れている様です.あくまでも私の感想ですが,フェニックス模型店製のパーツの窓の大きさはやや大きい様に感じます.もう一点の両者の差は前面と側面を繋ぐRの開始点と窓との位置関係です.キハ20系の運転台窓とRの開始点の間にはある程度の平面部があり,下の写真のように実車ではそれが光の当たり方によっては目立つのですがパーツでは運転台窓のHゴムとRの開始点までの距離が小さい(平面部が少ない)ように感じます.このことも窓の大きさが大きく感じる一つの要因であるとともに前面の表情が実物の印象と少し印象が異なる原因のようにも感じます.ただ私の製作した前面キハ25前面との差を意識したせいか平面部はあるものの窓の大きさがやや小さい様にも感じます.この辺りは寸法の設定が非常に難しく,今回キハ52は実際に車体を組み立てた際に窓の大きさが少し小さいように感じたため組み立て後に0.25㎜程度窓の大きさを大きく修正してあります.組み立て後のこのような修正はキットの形状を修正するより心理的なハードルも修正の難易度も自作車両の方が低いような気がします.しかし製作時に実物の印象に近づいたと判断しても真鍮地肌の状態と塗装後ではその印象が異なる場合もあります.そのためこの辺りの表現は出来上がった作品をよく観察して結果を評価し,その結果を反映しながら場数を踏んで改善していくしかない気もします.ただレファレンスとなる実物の印象も写真の光線状態や見る角度,Hゴムの色や塗色によって微妙に異なります.そう考えると製作の目的が正確な縮小による実物の再現ではなく,レイアウト上で実感的に(=それらしく?)見えるということであれば細かい寸法にあまり拘る必要もなく,今回製作したキハ52とキハ25の差は許容範囲で,今後改善すべきは塗り分け線の乱れ等もっと基本的な部分であるような気もします.
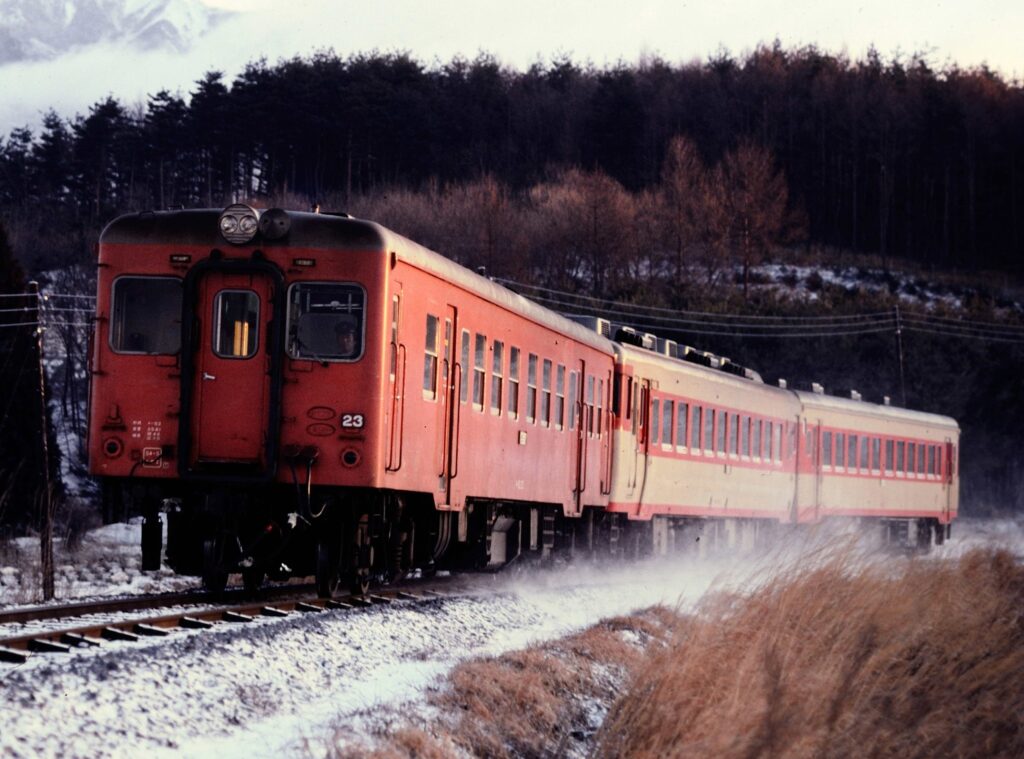
・ 窓周りの印象
今回真鍮版から車体の自作を行うにあたり真鍮版から車体を製作するに当たり過去製作した車体を見直し,過去製作した車体は窓の周囲は切断面を車体と垂直にヤスリ仕上げをしてあるため,それがプレス加工で窓周囲にプレスによるダレがあるバラキットと比較して実車の窓周りの実感を損ねているのではないかと考えました(記事はこちら).そこで今回は窓の周囲にヤスリでテーパーをつける加工を行いましたがその結果が下の写真です.
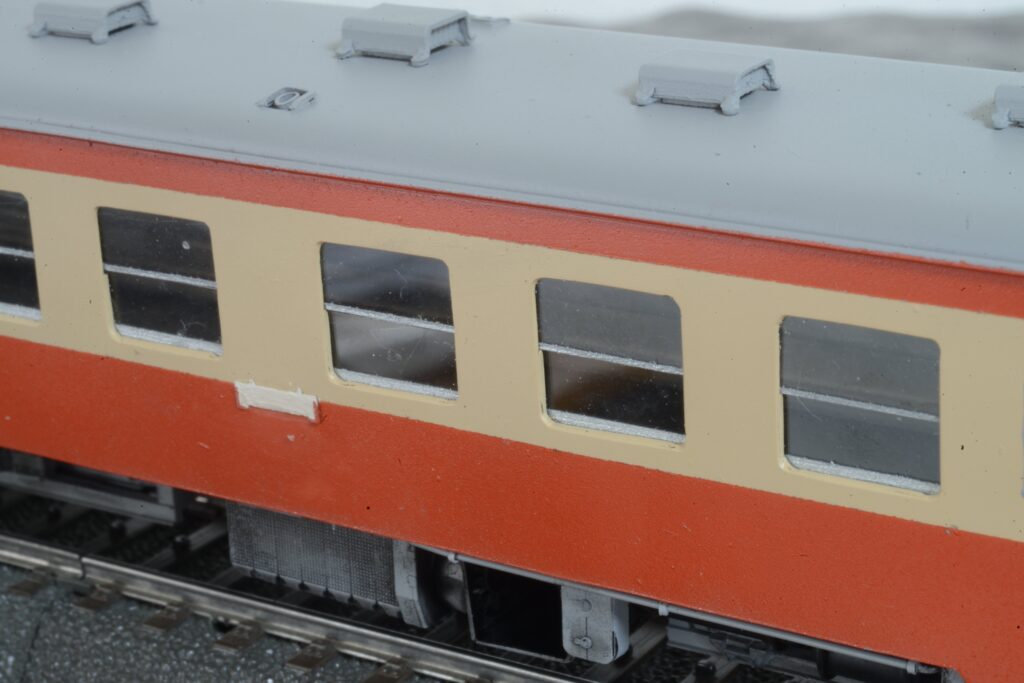
結果,このテーパー加工により今までの自作車体に比較すると窓周りの実感が増しており,当初の目論見通りの効果は認められました.その形状もバラキットに比較してより実物に近くバラキットと比較しても同等以上の効果はあったと思います.ただ,今回のキハ20系の場合,2段窓を表現するために窓の下半分(窓サッシの下段部分)には0.6㎜の厚さがあります,下の実写の写真と比較すると少し厚めである印象がある一方,側板に0.3㎜の真鍮板を使用した場合キハ55のような1段窓の場合は一番目立つ下辺のテーパー部の板厚が1/2になりますのでその際の効果については別途検討の余地があるような気もします.一方上の写真からも分かりますが詳細に観察すると貼り重ねた板と側板の境界面でハンダが十分に回り切っていない部分がありわずかに隙間が生じている部分がありました.ヤスリがけ直後にはめくれでわからない場合があるようですのでこの辺りは入念なチェックを徹底する必要があります.ヤスリがけはジグ等は用いず手作業で行いましたが,特に線の乱れが気になるようなところはありませんでした.
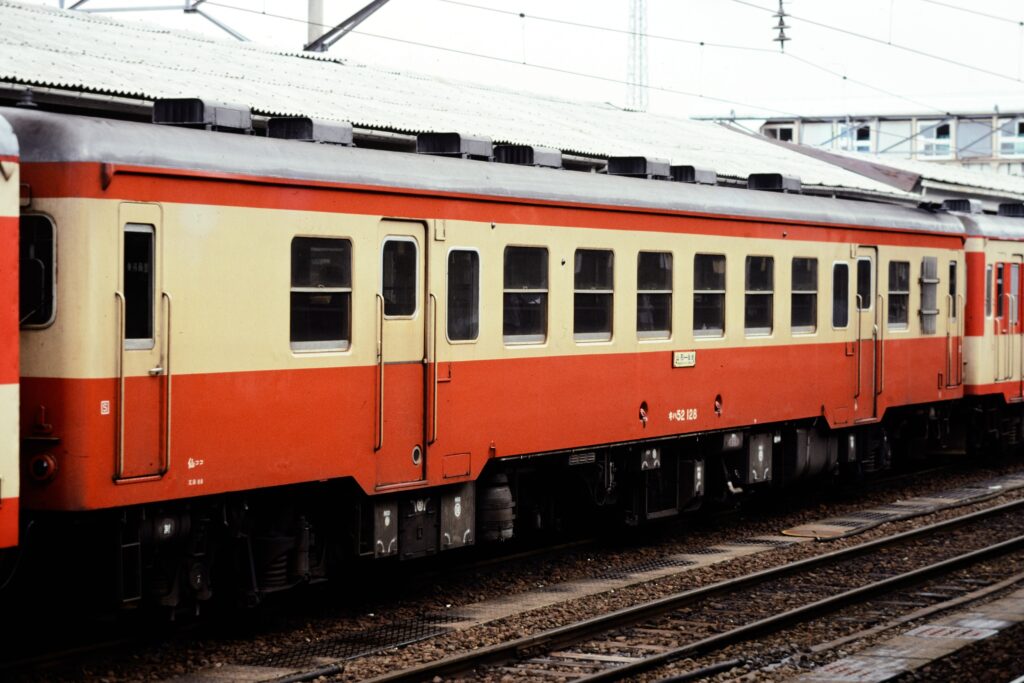
なお,今回,過去に真鍮版から車体を製作し,塗装が傷んでいた自作車体のキハユニ25 7の再塗装も行うこととし,その際に二重窓の周縁にわずかなテーパーをつけてみました.結果,つけたテーパーの量はわずかですがそれでもテーパーをつける前の車体と比較すると効果が認められます.ただ,この車体は0.4㎜厚の真鍮板を使用していますので厚さ0.3㎜の真鍮板を用いた車体では効果が多少異なるかもわかりません.
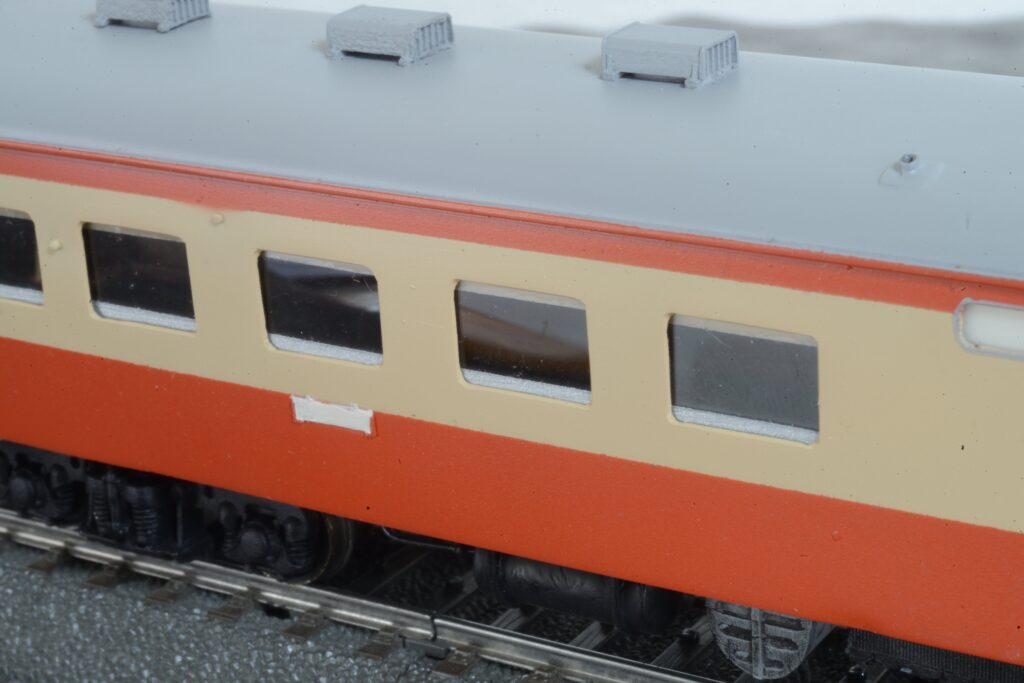
・ その他の細部(ヘッドライトレンズ)
上記の点を除いたディテーリング作業はバラキットと同一で使用しているパーツもほぼ同じあるため詳細は省略しますが,今回はヘッドライトのレンズを自作により作成しています.現在ヘッドライトレンズは色々なメーカーから各種直径のものが市販されていますが,今回のヘッドライトケースには(キットの付属品ではなく)市販の真鍮パイプを用ていますので径が適合するレンズがなさそうでした.このためレンズはエポキシ系接着剤により自作しました.その手順はまずヘッドライトケースに使用した真鍮パイプを輪切りにして並べ,その中に透明度の高いエポキシ系の接着剤を流し込んで完全に硬化する前にパイプからレンズを取り外し,硬化後耐水ペーパーでバリ取り・整形を行えば完成です.エポキシ系接着剤を流す際は気泡ができないように注意が必要ですが,細かい気泡がわずかに残っている程度であればレンズ面を細かい耐水ペーパーで磨き,レンズを「半透明化」すればほとんど目立たなくすることが可能です.なお,パイプを並べる際のベースは接着剤が簡単に剥がれる素材が必要ですので接着剤付属の撹拌用の板や撹拌用のヘラを使用しています.
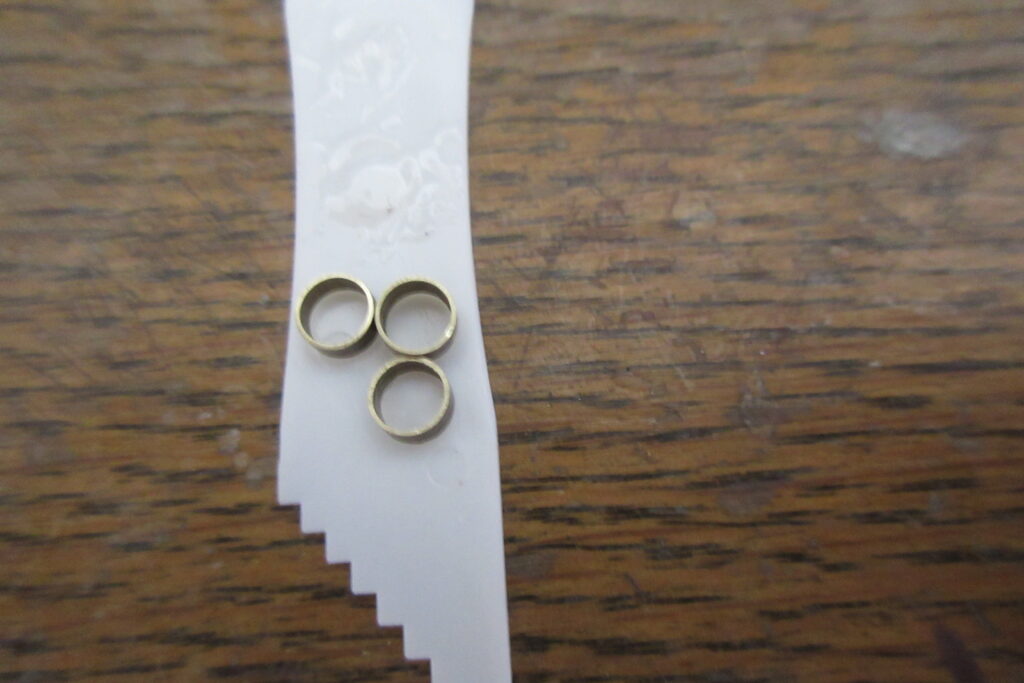
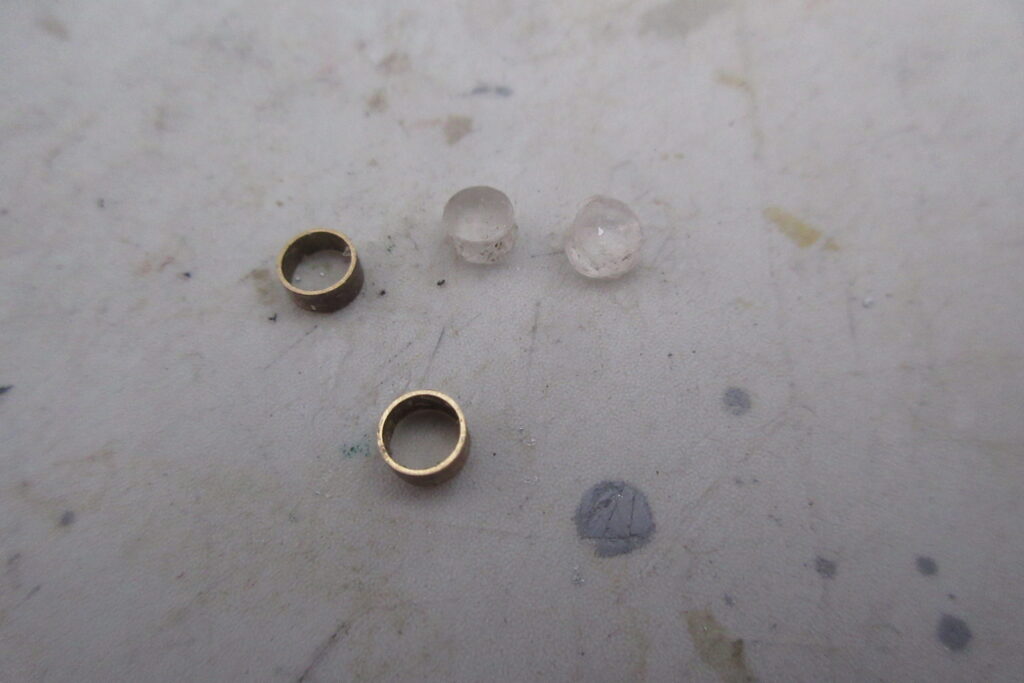
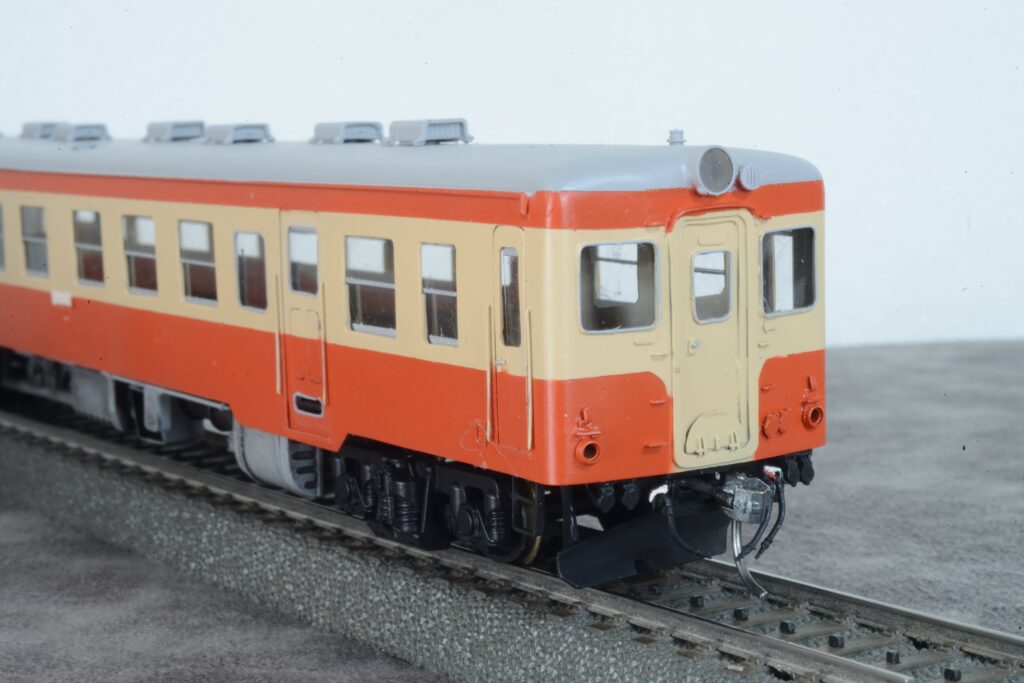
・ 床下機器のウエザリング
気動車の床下機器の塗色は大部分がグレーでエアータンク等の空気関係の機器が黒塗装となっています.このため私はまずグレーをラッカーで吹付塗装し,乾燥後にエナメル系塗料で空気関係機器に艶消し黒を筆塗りしています.一方気動車の床下は油や煤で結構な汚れがありますのでほとんどの場合(特に意図しない限り)ややきつめのウエザリングが必要となります.今まで私はこのウエザリングにエコーモデル製のウエザリングブラック,パステル,蝋燭の炎から集めた煤と王を使用してきたのですが,粉体によるウエザリングは触った際に手が汚れたり,レイアウト上に置いておくと埃が付着し時が経ってパウダーの上にホコリが付着すると埃を除去してもとなんとなく「汚い」状態となるため,パウダーによるウエザリングは以前からできれば避けたいと思っていました.しかし気動車の床下にはラッカー系塗料の他にエナメル系塗料で塗装された部分もあるため,エナメル系のスミ入れ塗料が使用できません.そこで今回は以前レイアウトを製作した際にウエザリングに使用したIndian Inkを使用してみました.結果は写真の通りで一通りのウエザリングは可能でしたがIndian Inkは乾燥が早く,一度乾燥すると容易に除去できませんので建物のような平面的な部分に使用する場合より取り扱いが難しく,この方法は墨入れ塗料によるウエザリングより難しいと感じました.そこで次回また気動車の床下を製作をする機会があったらその時は全体をラッカー塗装とした上でエアブラシによるウエザリングにも挑戦したいと思います.エアブラシによるウエザリングに関しては米国のModelrailroader誌にはその手法が定期的に掲載されており,Marklin社のInsider club向けの動画(Club film)の中でもウエザリングの過程が動画でよく紹介されていますので,これらを参考に気動車床下のウエザリングに関し,自分なりの手法が確立できればと思っております.
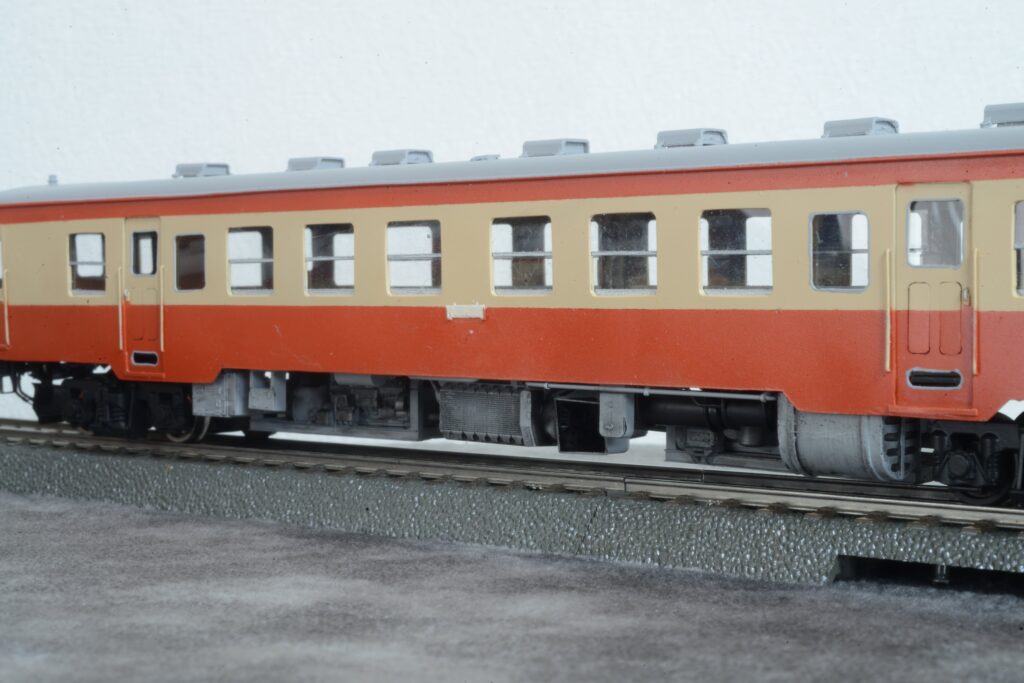
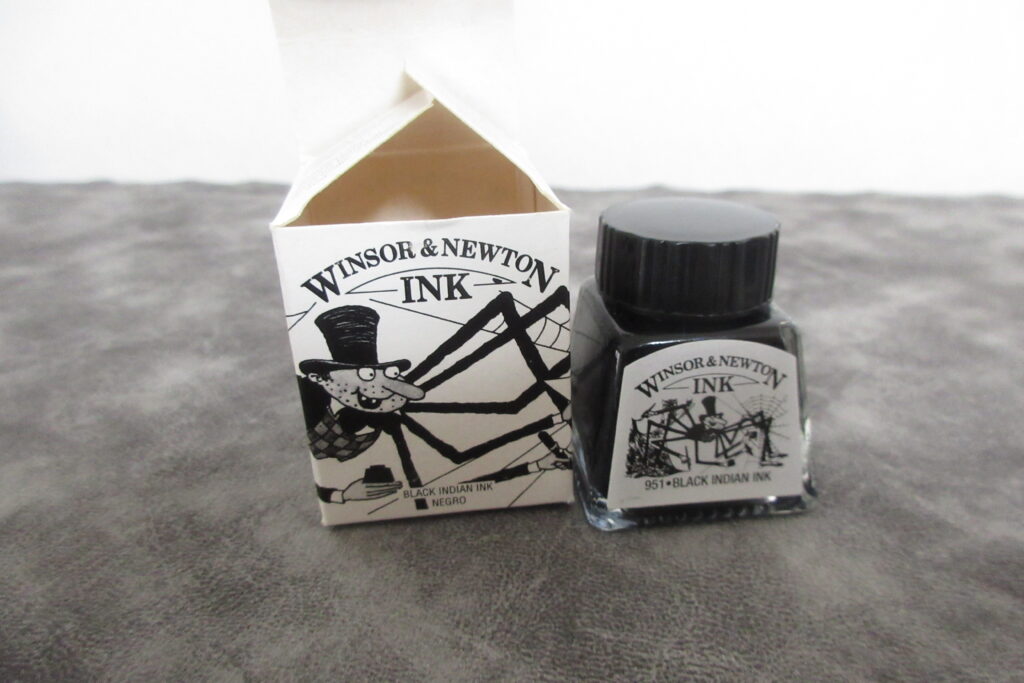
以上,簡単ですが今回真鍮板から製作したキハ52とキハ25に紹介を終わります.真鍮板からの車体製作は過去経験しているとはいえ実質上初めて経験することも多く当初は完成まで漕ぎ着けられるかどうかに自信がなく,早く一通りの工程を終えて結果を見たいという気持ちが優先して工作が雑になってしまったところも多々ありますが,今回何とか完成まで漕ぎ着けることができましたので,次回製作する際はより良い作品を目指して今回の反省を活かしてそのうちまたチャレンジしたいと思いっております.
最後までお読みいただきありがとうございました.